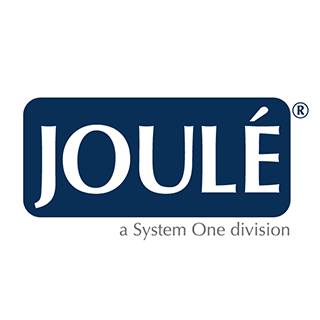
Senior Business Operations Engineer from Joulé
Denver, CO 80215
About the Job
Title: Senior Business Operations Engineer
Location: Lakewood, CO (hybrid 3 days / week onsite) - Relocation available
Schedule: M-F 8:00AM-5:00PM
Pay: $123,000.00 to $154,000.00/ year- Target Bonus on Base: 10%, inclusive relocation package for the right candidate (bonus, excellent healthcare benefits, unlimited PTO)
Type: Direct/Permanent
Start date: Immediate
Our client seeking a highly skilled and experienced Engineer 4 - Business Excellence (Quality) to join their team. This role is pivotal in enhancing their business operations and manufacturing processes through process improvement, Lean Six Sigma methodologies, and quality management systems. The ideal candidate will have over 8 years of experience in business operations with a focus on process improvement, demonstrated success in implementing quality programs, and a solid background in GMP manufacturing.
Key Responsibilities:
-
Continuous Improvement Projects:
- Utilize PDCA (Plan-Do-Check-Act) and DMAIC (Define-Measure-Analyze-Improve-Control) methodologies to drive continuous improvement projects aimed at enhancing product quality and services.
- Align quality management system processes with business requirements and strategic initiatives to develop impactful new processes across multiple disciplines.
-
Leadership and Guidance:
- Apply the E3 concept (Engage, Enable, Empower) in project activities to ensure sustainable improvements with the workforce, supervisors, and leaders.
- Provide leadership and mentorship to cross-functional managers to achieve site-specific improvements using Lean and continuous improvement methodologies.
-
Digital/Technology Transformation:
- Support digital and technology transformation efforts by contributing to value stream and process mapping to optimize new and existing processes and technologies.
- Lead the identification of Lean/Continuous Improvement needs in collaboration with business partners, develop implementation plans, and assess priorities.
Qualifications:
- Experience: A minimum of 8 years in business operations with a focus on process improvement. At least 2 years of demonstrated success in process improvement programs. GMP manufacturing experience required. Knowledge of FDA regulatory and ISO requirements for medical devices and drug combination products preferred.
- Certifications: Black Belt LEAN/Six Sigma certification preferred or must be obtained within the first year. Project management certification preferred.
- Technical Skills: Proficiency in Microsoft Teams, Excel, PowerPoint, Minitab (required), and Power BI (preferred).
- Skills & Competencies: Strong professional communication skills, proven leadership capabilities, and experience in developing and assessing both automated and manual assembly manufacturing processes.
Key Competencies:
- Proven ability to work on complex issues requiring detailed analysis and creative problem-solving.
- Expertise in mentoring less experienced engineers and providing oversight for the Quality Idea Generation Program.
- Ability to anticipate problems, generate advanced alternatives, and implement innovative solutions with significant business impact.
- Strong understanding of how process changes affect other areas and ability to manage the impact effectively.
Responsibilities Include:
- Performing audits and assessments to evaluate improvements and ensure consistency across global sites.
- Keeping updated on industry advancements and applying this knowledge to products and processes.
- Collaborating with key leaders and stakeholders to ensure cross-functional alignment within Quality.
- Identifying risks and managing multiple tasks/projects to avoid major delays in schedules or loss of business.
- Providing work direction and mentorship to technicians and junior engineers as needed.
#M3
#LI-GS1