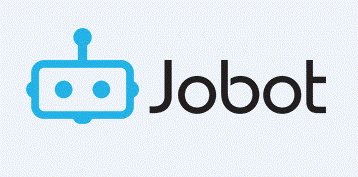
Quality Engineer at Jobot
Saint Charles, MO 63301
About the Job
Direct Hire Opportunity with Full Benefits. Excellent 401K matching!
This Jobot Job is hosted by: Brooke Meyer
Are you a fit? Easy Apply now by clicking the "Quick Apply" button
and sending us your resume.
Salary: $70,000 - $120,000 per year
A bit about us:
We specialize in design, engineering and manufacturing of electronic products. We help our clients by providing quality, dependable and innovative electronic controls at a great value.
Why join us?
Job Details
Job Objective: The Quality Engineer is under the direction of the Quality Manager and has responsibility for improving product and process quality and meeting all applicable product and process requirements. This responsibility includes supporting New Product Introduction quality targets, coordinating investigation of quality issues, issuing, and managing corrective actions, and working directly with suppliers through the production part approval process, change implementation, and issue investigation. The QE will work closely with Supply Chain and Engineering development teams, associates from Taiwan, PHMI, and all other affiliates.
Job Responsibilities:
1. Support quality planning in New Product Introduction process to mitigate risk of product quality defects.
2. Acts as a product development core-team member for quality and regulatory functions.
3. Participates in corrective action activities including evaluation of failure, investigation and root cause analysis, and countermeasure effectiveness assessments.
4. Develops, communicates, and monitors trends related to product quality and reliability.
5. Lead training programs consistent with organizational needs in accordance with current international ISO and CFR regulations.
6. Maintain records and documents in support of qualification activities (IQ/OQ/PQ/PPQ) and validation plans, e.g., manufacturing procedures, work instructions, design, and production guides, etc..
7. Ensures accurate and timely processing of quality records as needed.
8. Drafts and manages the quality systems documentation, procedures, instructions, forms pertaining to the assigned scope.
9. Extracts product and process information from databases and compiles metrics reports as requested.
10. Reviews all supplier, internal, and customer discrepancies; coordinate and track the effectiveness of corrective/preventive action (CAPA) efforts. Investigate causes of sporadic defects.
11. Performs internal audits and maintenance of the internal audit program to comply with ISO requirements.
12. Drafts and manages the quality systems documentation, procedures, instructions, and forms pertaining to the QMS scope.
13. Teach and train others on the tools for quality improvement such as flow charts, check sheets, pareto reports, histograms, cause-and-effect charts, scatter diagrams and controls charts.
14. Process ECO’s, Deviations, and NCMR’s
15. Interface and provide technical support on quality issues with the customer as needed.
16. Coordinate customer complaint investigations on items returned to the facility for analysis.
17. Accept responsibility and identify when additional authorization is required to resolve an issue by including management or others when appropriate.
18. Drive timely closure of all quality issues.
19. Performs other duties as assigned.
Supervisory Responsibilities: Only under special assignments within the quality department.
Knowledge, Skills and Abilities:
Interested in hearing more? Easy Apply now by clicking the "Quick Apply" button.
This Jobot Job is hosted by: Brooke Meyer
Are you a fit? Easy Apply now by clicking the "Quick Apply" button
and sending us your resume.
Salary: $70,000 - $120,000 per year
A bit about us:
We specialize in design, engineering and manufacturing of electronic products. We help our clients by providing quality, dependable and innovative electronic controls at a great value.
Why join us?
- Opportunity for growth and advancement
- Competitive Compensation and Benefits
- Collaborative work environment
- Stability
- Excellent 401 K match
- Paid time off
Job Details
Job Objective: The Quality Engineer is under the direction of the Quality Manager and has responsibility for improving product and process quality and meeting all applicable product and process requirements. This responsibility includes supporting New Product Introduction quality targets, coordinating investigation of quality issues, issuing, and managing corrective actions, and working directly with suppliers through the production part approval process, change implementation, and issue investigation. The QE will work closely with Supply Chain and Engineering development teams, associates from Taiwan, PHMI, and all other affiliates.
Job Responsibilities:
1. Support quality planning in New Product Introduction process to mitigate risk of product quality defects.
2. Acts as a product development core-team member for quality and regulatory functions.
3. Participates in corrective action activities including evaluation of failure, investigation and root cause analysis, and countermeasure effectiveness assessments.
4. Develops, communicates, and monitors trends related to product quality and reliability.
5. Lead training programs consistent with organizational needs in accordance with current international ISO and CFR regulations.
6. Maintain records and documents in support of qualification activities (IQ/OQ/PQ/PPQ) and validation plans, e.g., manufacturing procedures, work instructions, design, and production guides, etc..
7. Ensures accurate and timely processing of quality records as needed.
8. Drafts and manages the quality systems documentation, procedures, instructions, forms pertaining to the assigned scope.
9. Extracts product and process information from databases and compiles metrics reports as requested.
10. Reviews all supplier, internal, and customer discrepancies; coordinate and track the effectiveness of corrective/preventive action (CAPA) efforts. Investigate causes of sporadic defects.
11. Performs internal audits and maintenance of the internal audit program to comply with ISO requirements.
12. Drafts and manages the quality systems documentation, procedures, instructions, and forms pertaining to the QMS scope.
13. Teach and train others on the tools for quality improvement such as flow charts, check sheets, pareto reports, histograms, cause-and-effect charts, scatter diagrams and controls charts.
14. Process ECO’s, Deviations, and NCMR’s
15. Interface and provide technical support on quality issues with the customer as needed.
16. Coordinate customer complaint investigations on items returned to the facility for analysis.
17. Accept responsibility and identify when additional authorization is required to resolve an issue by including management or others when appropriate.
18. Drive timely closure of all quality issues.
19. Performs other duties as assigned.
Supervisory Responsibilities: Only under special assignments within the quality department.
Knowledge, Skills and Abilities:
- Bachelor’s Degree in a scientific discipline (i.e. Engineering); with at least two years of manufacturing or quality-related work experience
- Knowledge of quality measurement systems, statistical process control, and quality control
- Able to think proactively, locate opportunities and potential improvements, address and prevent problems
- Able to independently set priorities to meet organizational and departmental goals
- Ability to take initiative, maintain confidentiality, meet deadlines, and work in a team environment is essential.
- Excellent communication, teamwork, and collaboration skills
- Critical thinking and problem-solving skills
- Time sensitive (quickly responsive)
- Professional in manner, tact, and action.
- Proficient in Microsoft Office
Interested in hearing more? Easy Apply now by clicking the "Quick Apply" button.
Salary
70,000 - 120,000 /year