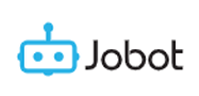
Maintenance Manager at Jobot
Davenport, IA 52808
About the Job
Maintenance Manager needed for well established global manufacturing company based in Davenport, IA
This Jobot Job is hosted by: David Hyon
Are you a fit? Easy Apply now by clicking the "Quick Apply" button
and sending us your resume.
Salary: $90,000 - $110,000 per year
A bit about us:
We are a leading top provider of metal sheet, plate, extrusions, and other innovative architectural products that support industries such as aerospace, automotive, building, and construction. We solve complex engineering challenges and transform the way we fly, drive and build.
Why join us?
Job Details
The Maintenance Manager will supervise an area of approximately 10 salaried resources including technicians, planners, and Team Leaders. The Maintenance Manager will oversee supervision through the team leaders of approximately 100 hourly resources including mechanics, machinists, roll grinders, and truck repair mechanics, and apprentices. The Manager will also support the plant’s craft training team in the development and execution of the apprenticeship programs within the central shops.
The Maintenance Manager will report to the Maintenance and Engineering Manager.
Machine Shop: The Maintenance Manager is accountable to provide the plant a machine repair and fabrication shop that supports unplanned and planned maintenance and engineering activities. The Manager will establish annual metrics that drive continuous improvement within the shop to provide this service safely and cost effectively. The Manager will also drive team maturity through direct reports.
Truck Repair Shop: The Maintenance Manager is accountable to manage the maintenance of the plant’s mobile equipment fleet. This will include continuous improvement in repair turnaround times, increase time in between failures, holding vendors accountable for equipment performance within warranty expectations, and driving cost reductions for the plant’s annual leasing and maintenance spend. The Manager will also drive team maturity through direct reports.
Roll Shops: The Maintenance Manager is accountable to manage the maintenance of the plant’s active and spare rolls. This includes continuous improvement in turnaround time for a roll assembly by driving reduction in grind and chocking/de-chocking standards, improved inspections through technology and roll grinder training, and improved quality control through training program. The Manager will also drive team maturity through direct reports.
Cost Control: The Maintenance Manager is accountable to lead and manage the plant’s MRO-SER and Energy cost savings initiative. This will also include the Central Maintenance and Engineering department cost savings initiative. Both the plant and department initiatives include achieving annual DI targets driven to deliver year over year spend reduction as a contributing factor in meeting the plant’s annual financial objectives.
EHS: The Maintenance Manager is accountable to manage the Central Maintenance and Engineering department environment and health and safety performance. This will include leading the department’s strategy for long term improvements as well as tactical day to day management with the other department Manager s. The Maintenance Manager will rely heavily on the EHS Coordinator to develop and deploy the strategy that will achieve the annual EHS objectives.
Competencies:
Ability to develop a strategic 5-year vision for the department – and then develop and execute long-term and short-term goals and plans to achieve it.
Ability to lead organizational change.
Excellent interpersonal skills.
Strong communication skills (both written and verbal).
Ability to communicate with all levels of the company including presenting proposals or providing business updates to executive leadership.
Results-oriented.
Ability to work in a matrix organization.
Ability to develop and coach employees on performance improvements and future career growth.
High level of technical/process expertise in a broad range of disciplines including:
Thermal operations and quality assurance
Labor relations
Ability to identify and implement cost reduction initiatives.
Activities:
Lead tactical maintenance through the staff.
Develop the department’s annual plans, objectives, and KPIs that enable the plant to meet its annual goals and long-term vision.
Establish a process with the staff to monitor, track and achieve annual goals each year.
Hold the team accountable to achieve objectives through the performance management process and system.
Develop business presentations that briefly illustrate the department’s performance and plans to expedite improvements where gaps exist.
Develop business proposals as needed for area of accountability to meet business goals.
Develop and maintain close working relationships with peers across the plant like Area Managers, Lead Area Managers, and Maintenance Department Managers
Interested in hearing more? Easy Apply now by clicking the "Quick Apply" button.
This Jobot Job is hosted by: David Hyon
Are you a fit? Easy Apply now by clicking the "Quick Apply" button
and sending us your resume.
Salary: $90,000 - $110,000 per year
A bit about us:
We are a leading top provider of metal sheet, plate, extrusions, and other innovative architectural products that support industries such as aerospace, automotive, building, and construction. We solve complex engineering challenges and transform the way we fly, drive and build.
Why join us?
- Stable and renown business over 100 years old
- Driven, hard working and dedicated colleagues
- Great benefits and long term career in Manufacturing
- Matching 401K (7% match)
- 5% bonuses paid quarterly
- Medical
- Dental
- Vision
Job Details
The Maintenance Manager will supervise an area of approximately 10 salaried resources including technicians, planners, and Team Leaders. The Maintenance Manager will oversee supervision through the team leaders of approximately 100 hourly resources including mechanics, machinists, roll grinders, and truck repair mechanics, and apprentices. The Manager will also support the plant’s craft training team in the development and execution of the apprenticeship programs within the central shops.
The Maintenance Manager will report to the Maintenance and Engineering Manager.
Machine Shop: The Maintenance Manager is accountable to provide the plant a machine repair and fabrication shop that supports unplanned and planned maintenance and engineering activities. The Manager will establish annual metrics that drive continuous improvement within the shop to provide this service safely and cost effectively. The Manager will also drive team maturity through direct reports.
Truck Repair Shop: The Maintenance Manager is accountable to manage the maintenance of the plant’s mobile equipment fleet. This will include continuous improvement in repair turnaround times, increase time in between failures, holding vendors accountable for equipment performance within warranty expectations, and driving cost reductions for the plant’s annual leasing and maintenance spend. The Manager will also drive team maturity through direct reports.
Roll Shops: The Maintenance Manager is accountable to manage the maintenance of the plant’s active and spare rolls. This includes continuous improvement in turnaround time for a roll assembly by driving reduction in grind and chocking/de-chocking standards, improved inspections through technology and roll grinder training, and improved quality control through training program. The Manager will also drive team maturity through direct reports.
Cost Control: The Maintenance Manager is accountable to lead and manage the plant’s MRO-SER and Energy cost savings initiative. This will also include the Central Maintenance and Engineering department cost savings initiative. Both the plant and department initiatives include achieving annual DI targets driven to deliver year over year spend reduction as a contributing factor in meeting the plant’s annual financial objectives.
EHS: The Maintenance Manager is accountable to manage the Central Maintenance and Engineering department environment and health and safety performance. This will include leading the department’s strategy for long term improvements as well as tactical day to day management with the other department Manager s. The Maintenance Manager will rely heavily on the EHS Coordinator to develop and deploy the strategy that will achieve the annual EHS objectives.
Competencies:
Ability to develop a strategic 5-year vision for the department – and then develop and execute long-term and short-term goals and plans to achieve it.
Ability to lead organizational change.
Excellent interpersonal skills.
Strong communication skills (both written and verbal).
Ability to communicate with all levels of the company including presenting proposals or providing business updates to executive leadership.
Results-oriented.
Ability to work in a matrix organization.
Ability to develop and coach employees on performance improvements and future career growth.
High level of technical/process expertise in a broad range of disciplines including:
Thermal operations and quality assurance
Labor relations
Ability to identify and implement cost reduction initiatives.
Activities:
Lead tactical maintenance through the staff.
Develop the department’s annual plans, objectives, and KPIs that enable the plant to meet its annual goals and long-term vision.
Establish a process with the staff to monitor, track and achieve annual goals each year.
Hold the team accountable to achieve objectives through the performance management process and system.
Develop business presentations that briefly illustrate the department’s performance and plans to expedite improvements where gaps exist.
Develop business proposals as needed for area of accountability to meet business goals.
Develop and maintain close working relationships with peers across the plant like Area Managers, Lead Area Managers, and Maintenance Department Managers
Interested in hearing more? Easy Apply now by clicking the "Quick Apply" button.
Salary
90,000 - 110,000 /year