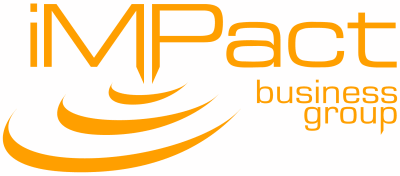
Maintenance Manager at Impact Business Group Inc
Canton, OH 44706
About the Job
Our client, an advanced, fully automated manufacturing facility in Canton, OH, is searching for a skilled Maintenance Manager to oversee and support a team of maintenance technicians. This role is pivotal to maintaining the plant's high standards of efficiency, reliability, and safety in a state-of-the-art environment where robots handle most production tasks. Ideal for an individual with solid technical expertise and leadership abilities, this opportunity provides a blend of hands-on troubleshooting and team management. Join a forward-thinking operation that values innovation, safety, and continuous improvement.
Key Responsibilities:
- Leadership & Team Development:
- Lead and support a team of maintenance technicians, electricians, and mechanics, ensuring efficient completion of daily tasks and ongoing development of their skills.
- Conduct regular performance reviews and provide coaching, training, and mentorship to foster growth and team cohesion.
- Coordinate with other departments to ensure maintenance activities align with broader organizational objectives.
- Maintenance Planning & Execution:
- Develop and implement preventative maintenance programs to enhance equipment performance and reduce downtime.
- Address and resolve complex issues involving mechanical, hydraulic, pneumatic, and electrical systems, including troubleshooting up to 480V, 3-phase electrical systems.
- Plan, prioritize, and schedule maintenance tasks to minimize impact on production schedules and keep operations running smoothly.
- Operational Support:
- Act as a key liaison between maintenance and production, responding quickly to breakdowns and coordinating effective repairs to support uninterrupted production.
- Ensure availability of essential spare parts and coordinate with procurement for timely replenishment.
- Monitor and adjust maintenance procedures to meet production requirements, ensuring minimal disruption.
- Safety Compliance & Audits:
- Uphold safety protocols and ensure all maintenance activities are carried out in accordance with safety standards and regulations.
- Conduct regular safety checks and inspections, identifying potential hazards and implementing corrective actions.
- Cultivate a culture of safety within the team and across maintenance operations, continually striving to improve safety practices.
- Budgeting & Cost Management:
- Manage the maintenance budget, overseeing expenses for labor, materials, and equipment.
- Prepare reports on maintenance activities, budget utilization, and equipment performance, and make recommendations for cost-effective practices.
- Collaborate with finance and operations teams to ensure maintenance spending aligns with organizational goals.
- Continuous Improvement & Process Optimization:
- Assess equipment performance data to identify areas for improvement and recommend upgrades or modifications.
- Participate in root cause analyses for equipment failures, working with cross-functional teams to implement corrective measures.
- Drive lean manufacturing initiatives and continuous improvement within the maintenance department to support overall plant efficiency.
Qualifications:
- High school diploma or equivalent required; Bachelor's degree in Engineering, Industrial Maintenance, or related field preferred.
- At least 5 years of supervisory experience in a maintenance role within a plastics or automotive manufacturing environment
- Strong troubleshooting skills, especially in hydraulics, pneumatics, and electrical systems (up to 480V, 3-phase).
- Familiarity with robotics and automated systems, particularly in a manufacturing or production setting.
Titles Encouraged to Apply:
- Maintenance Manager
- Lead Maintenance Technician
- Equipment Maintenance Supervisor
- Plant Maintenance Supervisor
- Maintenance Engineering Supervisor
- Mechanical Maintenance Supervisor
Salary
starting at 75,000 /year